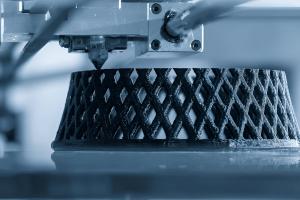
Industrial 3D printer creating a lattice-structured part, illustrating advanced additive manufacturing in action.
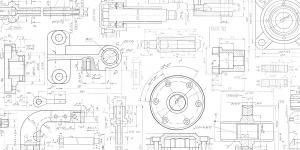
Close-up of technical mechanical drawings showing component blueprints, dimensions, and assembly schematics for manufacturing.
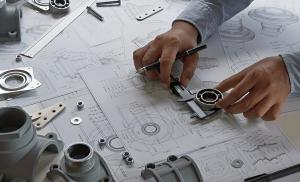
Engineer using calipers to measure a mechanical part over detailed technical drawings, surrounded by precision components and drafting tools.
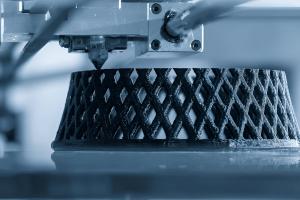
Industrial 3D printer creating a lattice-structured part, illustrating advanced additive manufacturing in action.
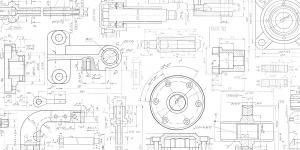
Close-up of technical mechanical drawings showing component blueprints, dimensions, and assembly schematics for manufacturing.
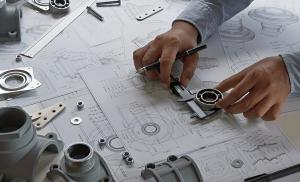
Engineer using calipers to measure a mechanical part over detailed technical drawings, surrounded by precision components and drafting tools.
Experience-driven Design for Manufacturability strategies from Tesla Mechanical Designs enable streamlined, cost-effective, and production-ready solutions.
The journey from a conceptual idea to a tangible, market-ready product is fraught with potential hurdles. Many organizations often grapple with unforeseen manufacturing complexities, escalating costs, and delays that can severely impact their bottom line and market position. Tesla Mechanical Designs, however, has meticulously honed its DFM philosophy to preempt these challenges, integrating manufacturability considerations into the very fabric of the design process. This proactive stance ensures that every design is innovative and high-performing and inherently optimized for efficient, cost-effective production.
𝐓𝐡𝐞 𝐈𝐦𝐩𝐨𝐫𝐭𝐚𝐧𝐜𝐞 𝐨𝐟 𝐃𝐞𝐬𝐢𝐠𝐧 𝐟𝐨𝐫 𝐌𝐚𝐧𝐮𝐟𝐚𝐜𝐭𝐮𝐫𝐚𝐛𝐢𝐥𝐢𝐭𝐲
𝐖𝐡𝐚𝐭 𝐈𝐬 𝐃𝐅𝐌?
Design for Manufacturability (DFM) is the engineering practice of designing products to be easily and economically manufactured. By integrating manufacturing considerations into the design phase, DFM minimizes production challenges, reduces costs, and ensures product quality.
𝐖𝐡𝐲 𝐃𝐅𝐌 𝐌𝐚𝐭𝐭𝐞𝐫𝐬
• Reduces Production Costs: Early identification of manufacturing challenges prevents expensive redesigns.
• Improves Product Quality: Streamlined designs lead to fewer defects and higher reliability.
• Accelerates Time-to-Market: Efficient designs shorten development cycles, giving companies a competitive edge.
• Enhances Collaboration: DFM fosters communication between design, engineering, and manufacturing teams.
𝐎𝐩𝐭𝐢𝐦𝐢𝐳𝐢𝐧𝐠 𝐟𝐨𝐫 𝐏𝐫𝐨𝐝𝐮𝐜𝐭𝐢𝐨𝐧: 𝐓𝐞𝐬𝐥𝐚 𝐌𝐞𝐜𝐡𝐚𝐧𝐢𝐜𝐚𝐥 𝐃𝐞𝐬𝐢𝐠𝐧𝐬’ 𝐏𝐫𝐨𝐯𝐞𝐧 𝐀𝐩𝐩𝐫𝐨𝐚𝐜𝐡
At the core of Tesla Mechanical Designs' DFM methodology lies a holistic and meticulous approach to optimizing every facet of the production process. The firm understands that efficiency is not achieved through isolated improvements but through a synergistic integration of design elements. This involves a profound understanding of how material selection, tolerance optimization, and assembly simplification collectively contribute to a streamlined and robust manufacturing pipeline.
"Our commitment to DFM is unwavering," states a representative from Tesla Mechanical Design. "We don't just design; we engineer for Manufacturability. This means that from the moment a concept takes shape, we rigorously evaluate material properties, consider manufacturing processes, and envision the assembly sequence. It's about designing intelligence into the product from day one.” Said Divya Dave, Assistant Director at Tesla Mechanical Designs.
Tesla Mechanical Designs’ reputation as an industry leader is rooted in its commitment to optimizing every aspect of the product development process for Manufacturability. Their approach is built on three core pillars:
𝟏. 𝐌𝐚𝐭𝐞𝐫𝐢𝐚𝐥 𝐒𝐞𝐥𝐞𝐜𝐭𝐢𝐨𝐧
Choosing the right material is fundamental to both product performance and Manufacturability. Tesla Mechanical Designs’ engineers:
• Evaluate material properties (strength, weight, durability, cost) to meet product requirements.
• Consider availability and lead times to prevent supply chain delays.
• Assess environmental impact and recyclability for sustainable manufacturing.
• Recommend alternatives in case of supply disruptions or cost fluctuations.
𝟐. 𝐓𝐨𝐥𝐞𝐫𝐚𝐧𝐜𝐞 𝐎𝐩𝐭𝐢𝐦𝐢𝐳𝐚𝐭𝐢𝐨𝐧
Overly tight tolerances can dramatically increase manufacturing costs and complexity. Tesla Mechanical Designs:
• Analyzes functional requirements to determine where tight tolerances are essential.
• Uses advanced simulation tools to predict how variations affect assembly and performance.
• Works with suppliers to ensure tolerances are achievable with standard processes, reducing the need for costly custom tooling.
• Balances performance, cost, and Manufacturability for optimal outcomes.
𝟑. 𝐀𝐬𝐬𝐞𝐦𝐛𝐥𝐲 𝐒𝐢𝐦𝐩𝐥𝐢𝐟𝐢𝐜𝐚𝐭𝐢𝐨𝐧
Complex assemblies increase manufacturing time and introduce more opportunities for error. Tesla Mechanical Designs:
• Applies design principles such as modularity and part reduction to simplify assembly.
• Designs for automated assembly reduce labor costs and increase consistency.
• Incorporates features like snap-fits, self-locating parts, and standardized fasteners to streamline processes.
• Conducts assembly simulations to identify and eliminate bottlenecks before production begins.
𝐄𝐚𝐫𝐥𝐲 𝐈𝐧𝐭𝐞𝐠𝐫𝐚𝐭𝐢𝐨𝐧 𝐟𝐨𝐫 𝐌𝐚𝐱𝐢𝐦𝐮𝐦 𝐈𝐦𝐩𝐚𝐜𝐭
𝐓𝐡𝐞 𝐕𝐚𝐥𝐮𝐞 𝐨𝐟 𝐄𝐚𝐫𝐥𝐲 𝐃𝐅𝐌 𝐈𝐧𝐭𝐞𝐠𝐫𝐚𝐭𝐢𝐨𝐧
One of the most critical differentiators of Tesla Mechanical Designs’ approach is its unwavering commitment to integrating manufacturability considerations from the absolute initial stages of the design process. Many companies err by treating DFM as an afterthought, attempting to shoehorn manufacturing considerations into a nearly finalized design. This reactive approach almost invariably leads to costly redesigns, extensive tooling modifications, and significant delays in time-to-market.
"The greatest impact of DFM is achieved when it is integrated from the first sketch, the initial concept," emphasizes the representative. "Waiting until a design is mature to consider how it will be manufactured is a recipe for frustration and financial drain. Our philosophy is about being proactive, about building Manufacturability into the DNA of the product.", said Prex Poojara, Director at Tesla Mechanical Designs.
Tesla Mechanical Designs engages with clients early in the product development lifecycle, often during the conceptualization and feasibility study phases. This early involvement allows their experienced engineers to identify potential manufacturing challenges and opportunities for optimization before design decisions become entrenched. By leveraging advanced simulation tools, virtual prototyping, and their extensive knowledge of various manufacturing processes, they can predict how a design will perform on the production line, long before any physical prototypes are built. This foresight enables them to make informed design choices that preclude costly retooling, material waste, and production bottlenecks. The savings in time and money realized through this early integration are often substantial, providing clients with a significant competitive advantage. This proactive stance significantly reduces development cycles, accelerates market entry, and maximizes return on investment.
𝐇𝐨𝐰 𝐄𝐚𝐫𝐥𝐲 𝐃𝐅𝐌 𝐒𝐚𝐯𝐞𝐬 𝐓𝐢𝐦𝐞 𝐚𝐧𝐝 𝐌𝐨𝐧𝐞𝐲
• Fewer Design Iterations: Potential manufacturing issues are identified and resolved before prototypes are built.
• Reduced Tooling Costs: Designs are optimized for standard manufacturing methods, minimizing the need for custom tools.
• Shorter Development Cycles: Efficient designs move smoothly from CAD to production, avoiding delays.
• Improved Supplier Engagement: Early involvement of manufacturing partners ensures designs are feasible and cost-effective.
𝐑𝐞𝐚𝐥-𝐖𝐨𝐫𝐥𝐝 𝐄𝐱𝐚𝐦𝐩𝐥𝐞
A client approached Tesla Mechanical Designs with a complex enclosure requiring tight tolerances and multiple assembly steps. By engaging early, Tesla’s team:
• Recommended a material with better dimensional stability.
• Simplified the assembly from six parts to three, reducing labor and potential failure points.
• Optimized tolerances to align with standard injection molding capabilities.
The result: a 20% reduction in production costs and a faster product launch.
𝐓𝐞𝐬𝐥𝐚 𝐌𝐞𝐜𝐡𝐚𝐧𝐢𝐜𝐚𝐥 𝐃𝐞𝐬𝐢𝐠𝐧𝐬’ 𝐃𝐅𝐌 𝐁𝐞𝐬𝐭 𝐏𝐫𝐚𝐜𝐭𝐢𝐜𝐞𝐬
Tesla Mechanical Designs’ expertise is built on proven best practices. These guidelines help clients avoid common pitfalls and achieve robust, cost-effective designs.
𝟏. 𝐂𝐨𝐥𝐥𝐚𝐛𝐨𝐫𝐚𝐭𝐢𝐯𝐞 𝐃𝐞𝐬𝐢𝐠𝐧 𝐑𝐞𝐯𝐢𝐞𝐰𝐬
• Regular cross-functional design reviews ensure all stakeholders—design, engineering, manufacturing, and quality—are aligned.
• Feedback loops catch potential issues early, reducing the risk of late-stage changes.
𝟐. 𝐒𝐭𝐚𝐧𝐝𝐚𝐫𝐝𝐢𝐳𝐚𝐭𝐢𝐨𝐧
• Preference for standard components and processes wherever possible.
• Reduces lead times, simplifies inventory, and lowers costs.
𝟑. 𝐃𝐞𝐬𝐢𝐠𝐧 𝐟𝐨𝐫 𝐀𝐬𝐬𝐞𝐦𝐛𝐥𝐲 (𝐃𝐅𝐀)
• Focus on minimizing the number of parts and assembly steps.
• Use of self-locating and self-fastening features to reduce assembly errors.
𝟒. 𝐏𝐫𝐨𝐭𝐨𝐭𝐲𝐩𝐢𝐧𝐠 𝐚𝐧𝐝 𝐓𝐞𝐬𝐭𝐢𝐧𝐠
• Rapid prototyping to validate design choices before committing to production tooling.
• Early testing identifies potential issues, enabling quick iteration.
𝟓. 𝐒𝐮𝐩𝐩𝐥𝐢𝐞𝐫 𝐄𝐧𝐠𝐚𝐠𝐞𝐦𝐞𝐧𝐭
• Early and ongoing communication with suppliers ensures designs are practical and cost-effective.
• Supplier feedback is incorporated into design decisions, preventing costly surprises.
𝐀𝐯𝐨𝐢𝐝𝐢𝐧𝐠 𝐂𝐨𝐦𝐦𝐨𝐧 𝐃𝐅𝐌 𝐏𝐢𝐭𝐟𝐚𝐥𝐥𝐬
Even experienced teams can fall into traps that increase costs and delay projects. Tesla Mechanical Designs helps clients avoid these pitfalls:
• Over-Engineering: Adding unnecessary features or complexity that increase costs without adding value.
• Ignoring Manufacturing Constraints: Designing parts that cannot be easily produced with available processes.
• Late DFM Consideration: Waiting until after design completion to address Manufacturability, leading to expensive redesigns.
• Poor Documentation: Incomplete or unclear drawings and specifications that cause confusion and errors in production.
𝐀𝐜𝐡𝐢𝐞𝐯𝐢𝐧𝐠 𝐑𝐨𝐛𝐮𝐬𝐭, 𝐂𝐨𝐬𝐭-𝐄𝐟𝐟𝐞𝐜𝐭𝐢𝐯𝐞 𝐃𝐞𝐬𝐢𝐠𝐧𝐬
Tesla Mechanical Designs’ holistic approach to DFM delivers tangible results:
• Lower Production Costs: Through material optimization, tolerance management, and assembly simplification.
• Higher Product Quality: Designs are robust, reliable, and easier to manufacture.
• Faster Time-to-Market: Early DFM integration streamlines development and production.
• Stronger Supplier Relationships: Collaborative processes ensure smooth transitions from design to manufacturing.
Design for Manufacturability is not just a technical requirement—it is a strategic advantage. Tesla Mechanical Designs empowers clients to unlock efficiency at every stage of product development, from concept to mass production. By prioritizing material selection, tolerance optimization, assembly simplification, and early DFM integration, Tesla Mechanical Designs ensures every product is ready for efficient, cost-effective manufacturing.
For organizations seeking to minimize risk, reduce costs, and accelerate innovation, Tesla Mechanical Designs is the expert resource for DFM. Their actionable insights and best practices help clients avoid common pitfalls and achieve lasting success in the marketplace.
𝐀𝐛𝐨𝐮𝐭 𝐓𝐞𝐬𝐥𝐚 𝐌𝐞𝐜𝐡𝐚𝐧𝐢𝐜𝐚𝐥 𝐃𝐞𝐬𝐢𝐠𝐧𝐬
Tesla Mechanical Designs is a leading provider of mechanical engineering solutions, specializing in Design for Manufacturability (DFM) across various industries. With a team of experienced engineers and a proven track record of success, Tesla Mechanical Designs transforms ideas into market-ready products through innovative, efficient, and practical design solutions. For more information or to schedule a consultation, contact Tesla Mechanical Designs - https://www.teslamechanicaldesigns.com/contact-us.php or Visit our official website - https://www.teslamechanicaldesigns.com
Divya Dave
Tesla Mechanical Designs
+1 214-699-6163
email us here
Visit us on social media:
LinkedIn
Bluesky
Instagram
Facebook
X
Other
Legal Disclaimer:
EIN Presswire provides this news content "as is" without warranty of any kind. We do not accept any responsibility or liability for the accuracy, content, images, videos, licenses, completeness, legality, or reliability of the information contained in this article. If you have any complaints or copyright issues related to this article, kindly contact the author above.
